The management of customer data is very important in every company. Supplier relationship management, on the other hand, is less developed. It's different for us. Years ago we started setting up a CSR supplier management system. This documents the degree of implementation of sustainability in our value chain. During the last inquiries with our suppliers, we turned the tables and asked them about the integrity of Dibella as a customer.
Bet you can have comprehensive information about your customers displayed on the screen at the touch of a button? Duration of the business relationship, order history, complaints and the name of your contact person - these and many other data have been stored for years in order to make the connection with the customer more transparent and traceable.
But do you know your suppliers as well as your customers? We have asked ourselves this question not just since our first Green Button certification, but much earlier. Because if you want to offer a responsible value chain, you have to know it. That's why we started years ago to take a closer look at the social and ecological conditions of our supply partners, to exclude certain things such as subcontracting through our Code of Conduct and to store this information in an in-house system. More and more data has been added through on-site visits and audits, so that we now have a very precise overview of our suppliers.
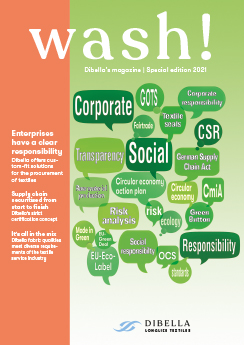
In 2021 we already made a special about CSR.
On the occasion of the re-certification with the “Green Button 2.0”, we recently started a new query with our suppliers. In line with our policy to promote living wages in the supply chain, we have asked for disclosure of garment manufacturing wages, broken down by female and male employees and broken down by qualification. Based on the data received, we created an initial wage gap analysis between the real wage paid by our suppliers to their employees - often the government-paid minimum wage - and the living wage calculated for the region. In addition, we wanted to know how high the capacity utilization of the companies is due to Dibella orders and whether this results in a dependency relationship. And it is precisely from this topic that we wanted to systematically record what is important to our suppliers when working together. Do you urgently need our orders, are our lead times and delivery times sufficient for production planning and how do you rate our communication culture? So we came up with the idea of a supplier survey. Here our partners were able to address different aspects of our collaboration and express additional wishes. We were very pleased with the results of the survey: Overall, our production partners are very satisfied with us as customers. But that doesn't mean we rest on our laurels. Because good things can always be made a little better!
With the information from our suppliers, we now have a profound background knowledge of industrial processing. The risks to responsible textile production can also lie outside the factory walls - for example when people are forced to work in cotton fields. To identify such negative factors, we analyze possible country-, material- and industry-specific risks at least once a year and, if necessary, as appropriate, evaluate and prioritize them and initiate preventive measures. And even though we are very well positioned thanks to our risk and supplier management, things can still be a little better. That is our declared goal!